The production plant
All stages of production take place within the company, in an area of 9000 m²
A recently renovated and expanded production plant, an area of 9000 m² and 140 employees make up the innovative and avant-garde structure that has always represented the work of ARS Elettromeccanica and which allows the company to carry out an efficient internal production process.
All products developed within our production plant take into account the requirements of various national and international regulations. We support our customers by also assisting them in the homologation or certification process of the various devices.
There are two main production areas: coils and solenoid pumps
Study and design of the coils follow the specific requests of the Customers, with the aim of finding the most appropriate and functional solutions from a technical and qualitative point of view. All production phases of the coils (winding, welding, encapsulation and 100% testing) take place within the company through the use of automated machines and lines.
Part of the production of coils is used internally for the construction of different types of solenoid pumps: high pressure CP and SMART pumps, low pressure MPP pumps and high flow PI pumps. The production, assembly and complete testing of the solenoid pumps also takes place internally, using automatic assembly lines.

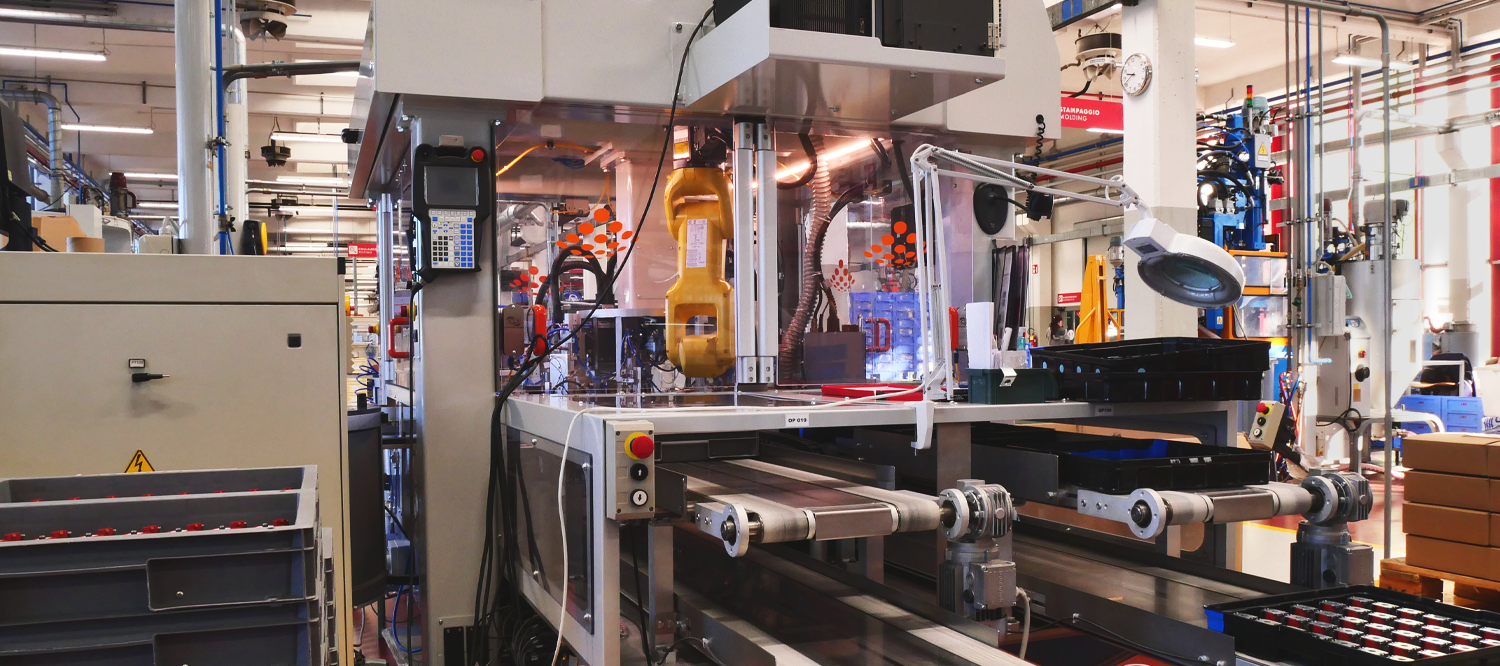


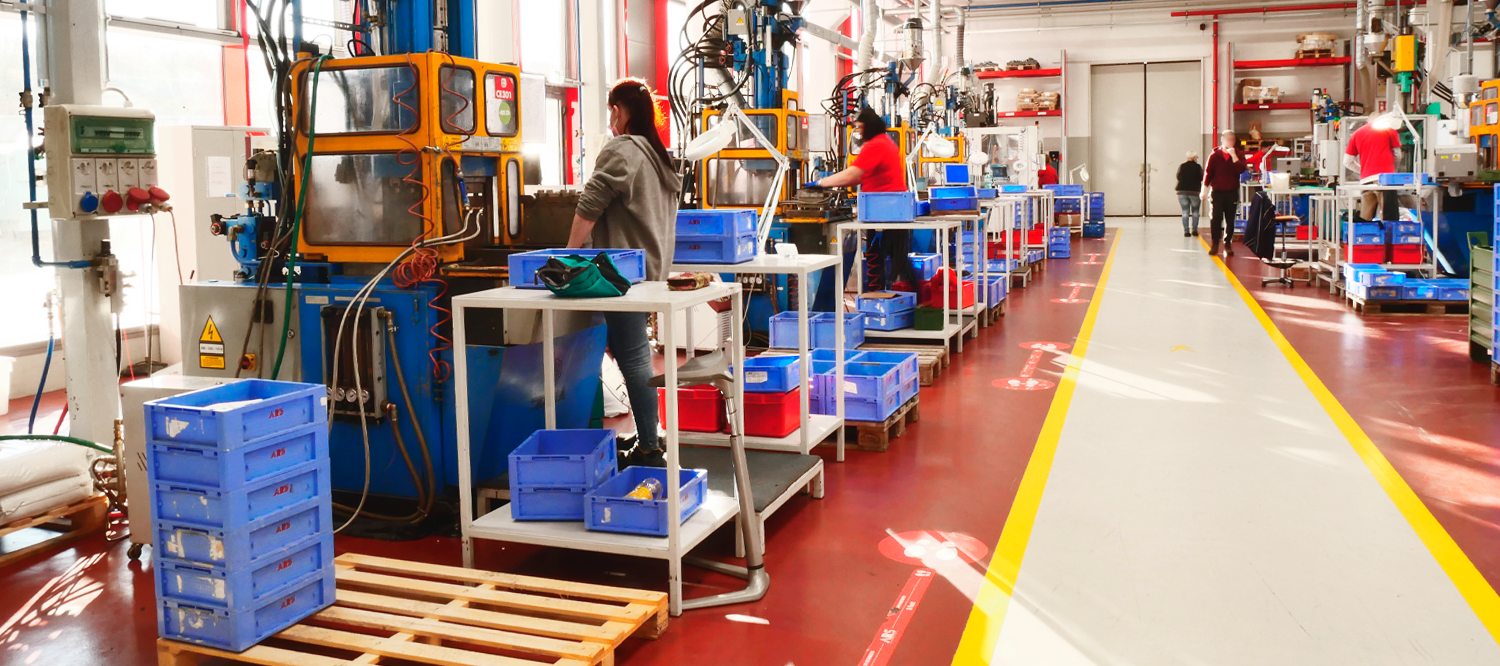



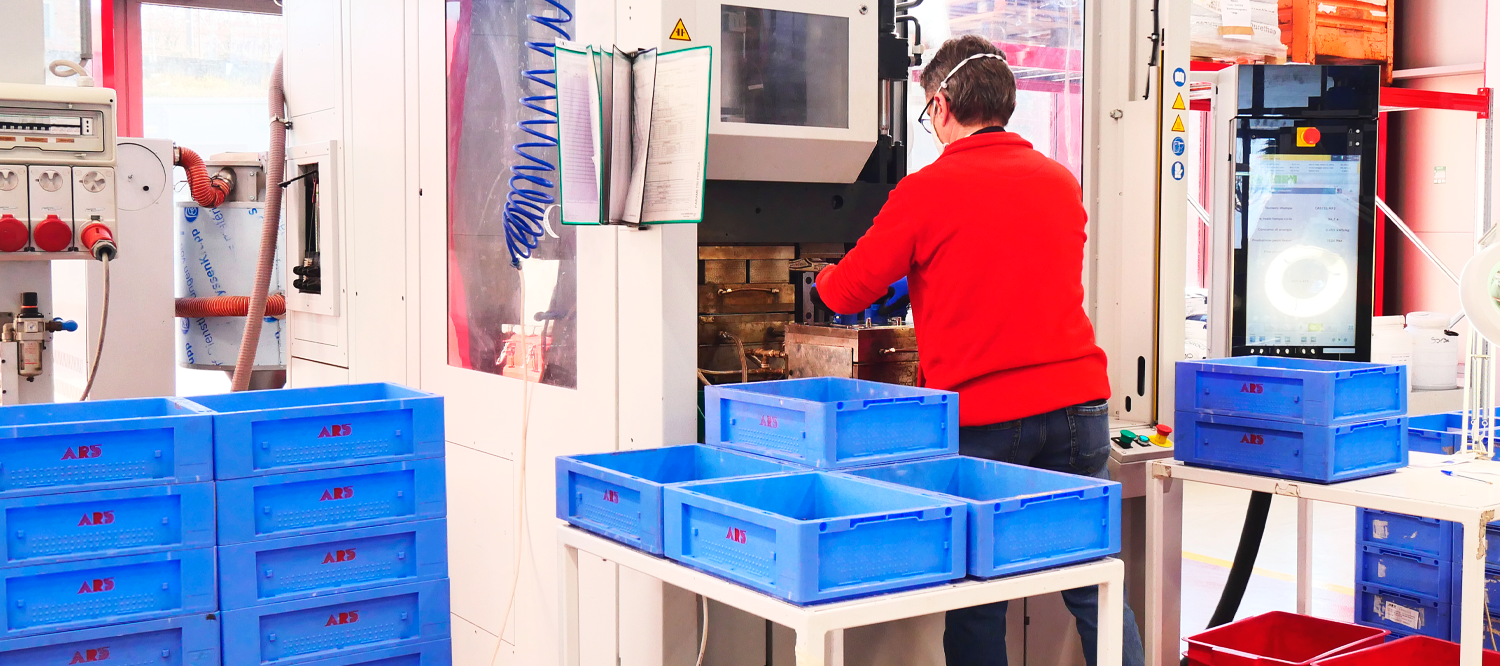
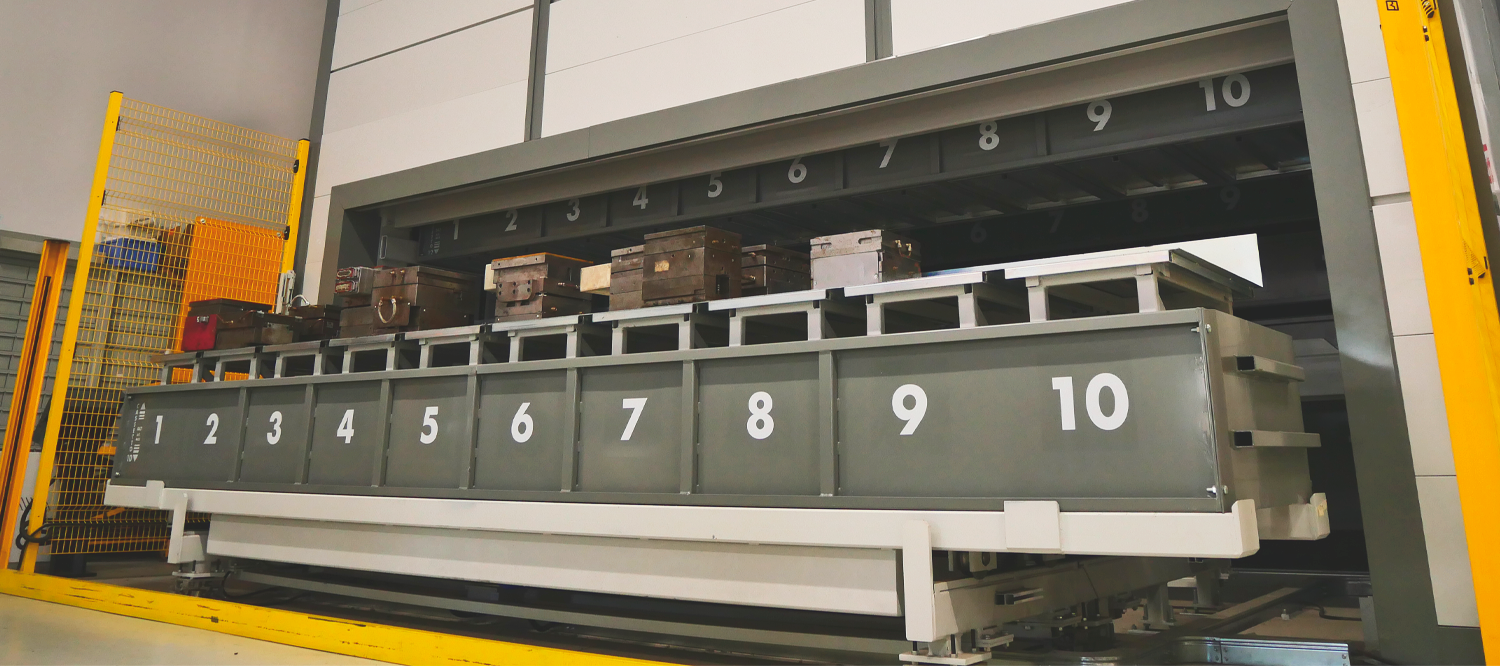
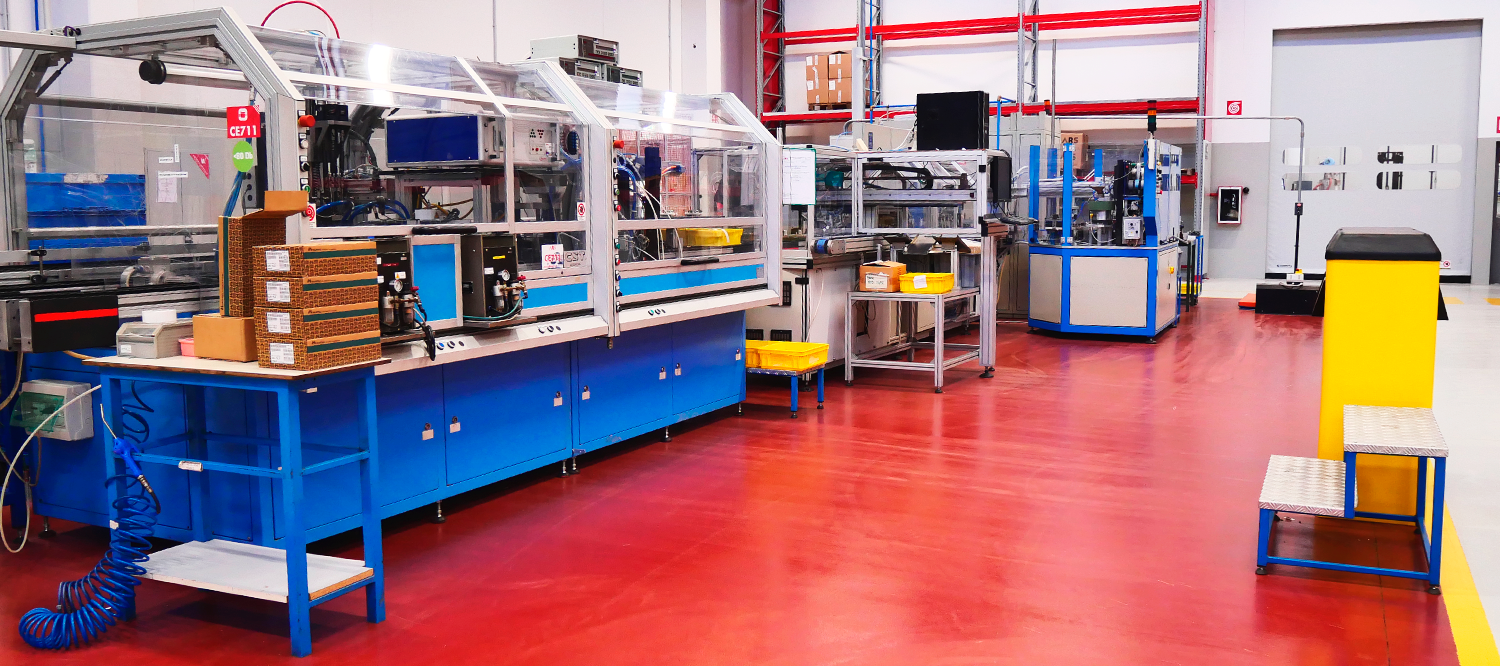
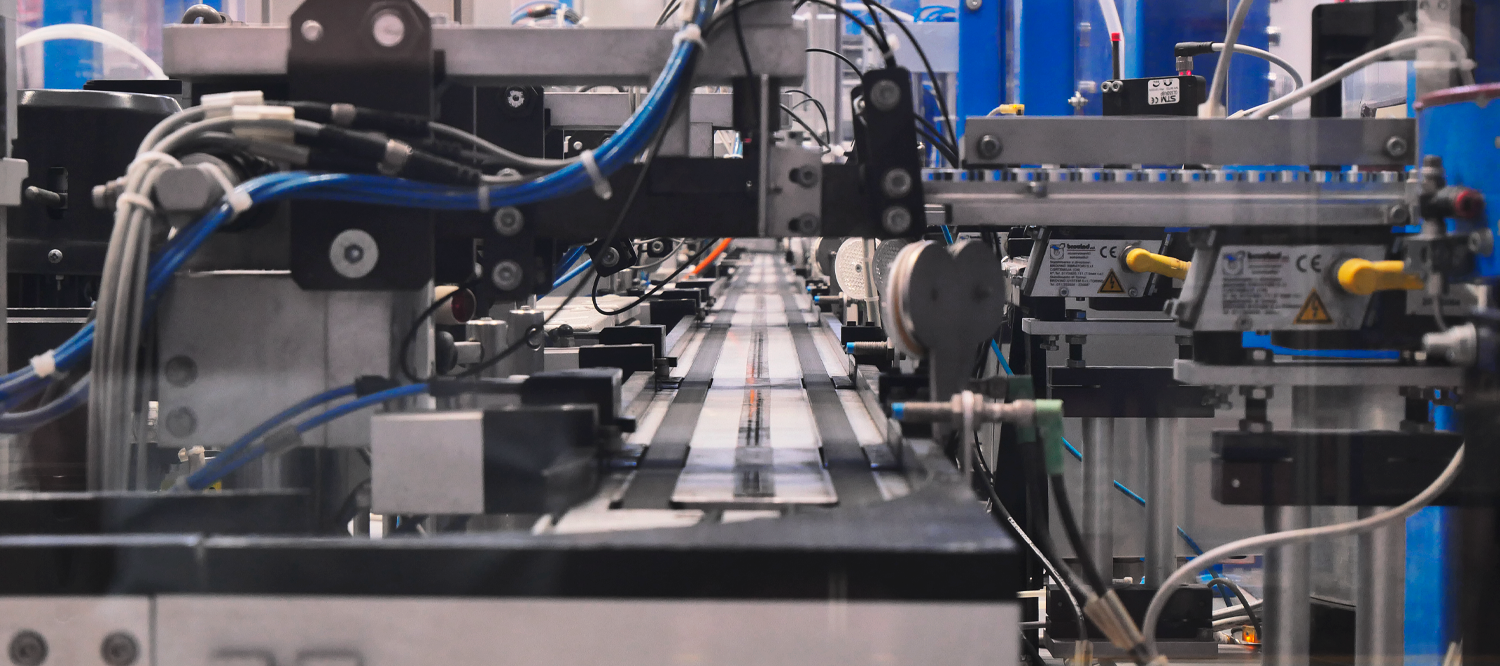
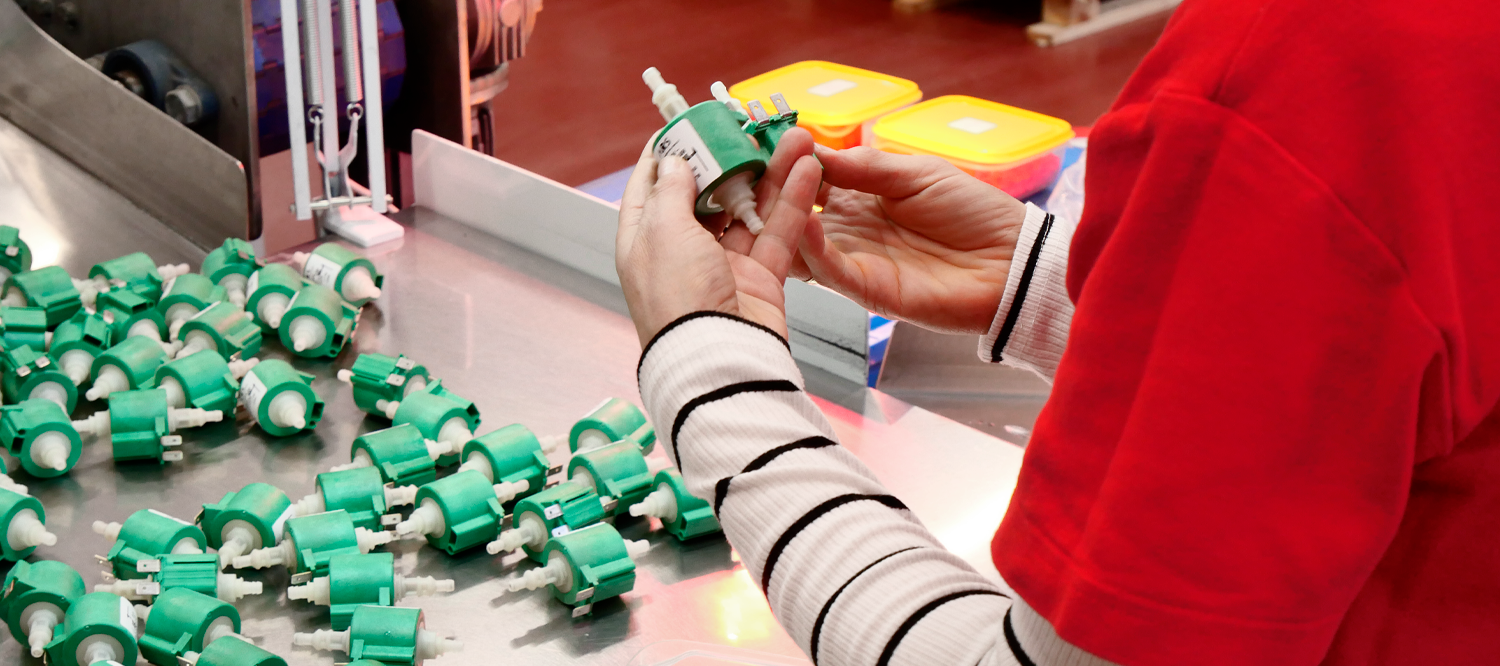
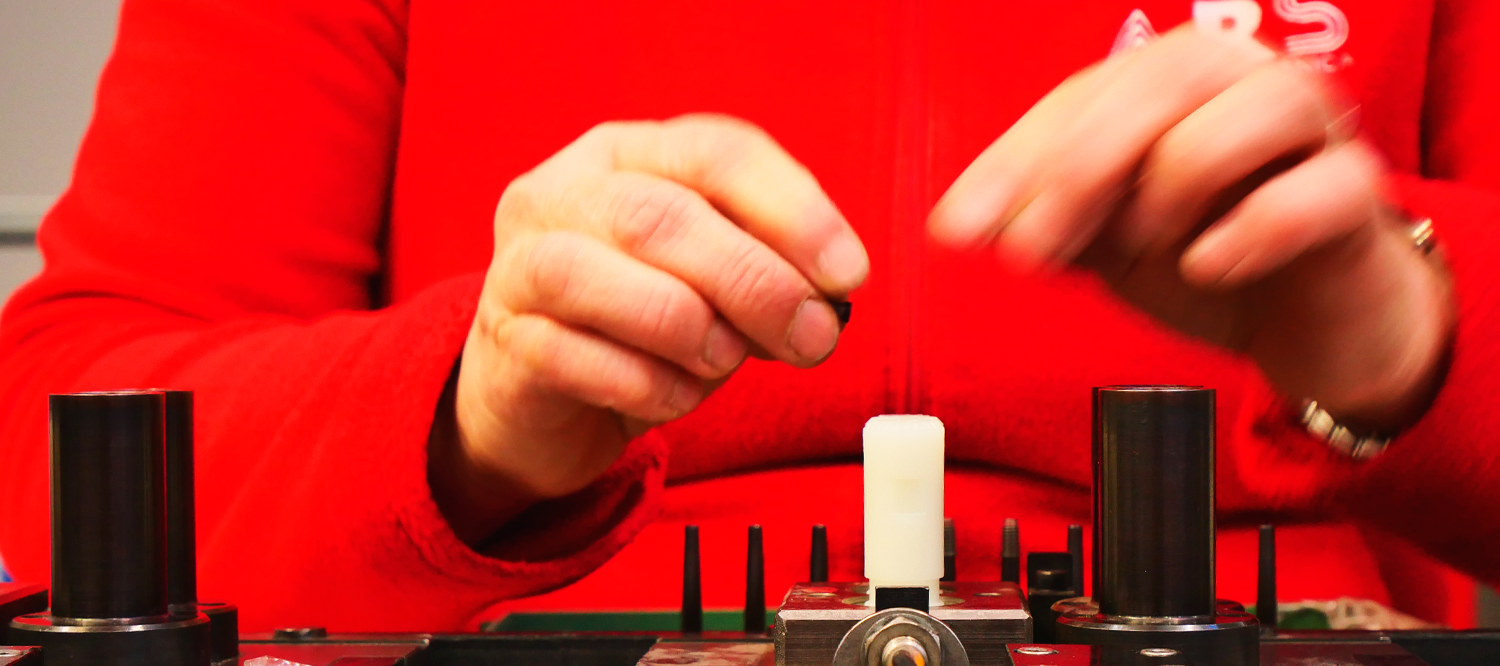
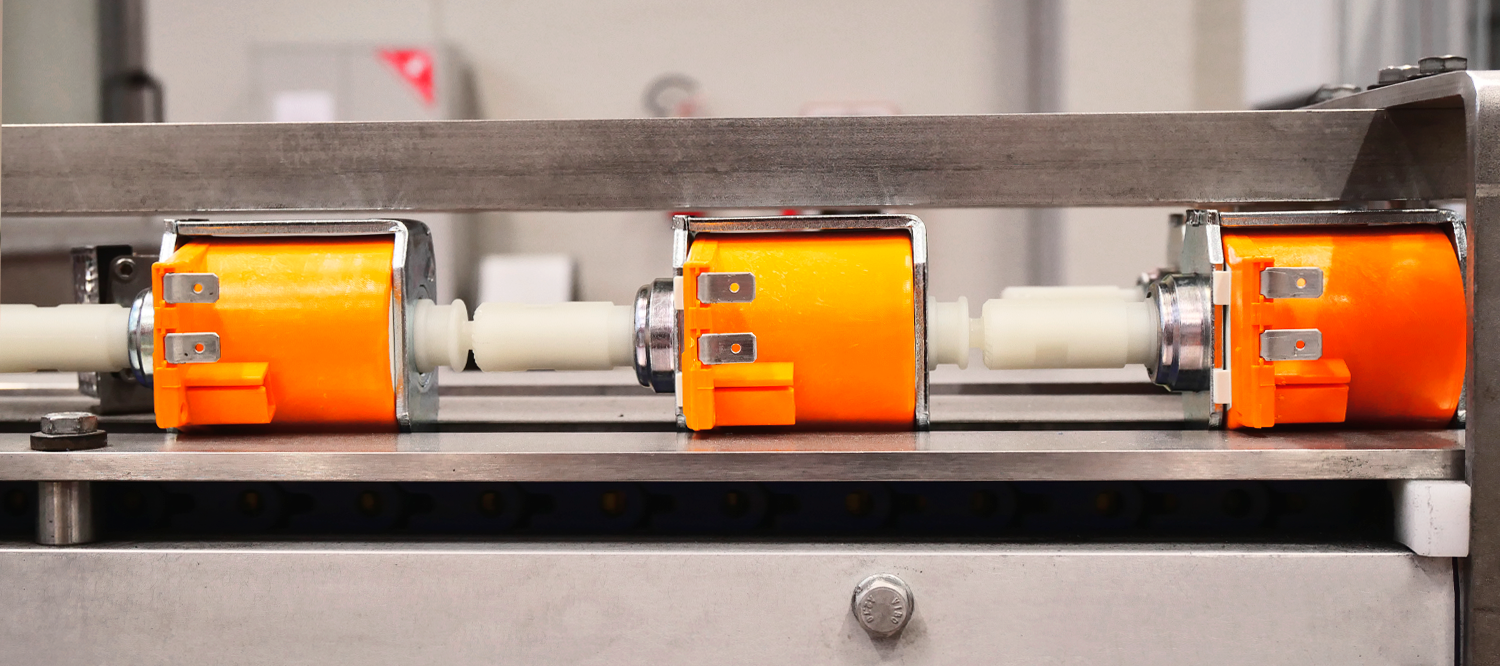
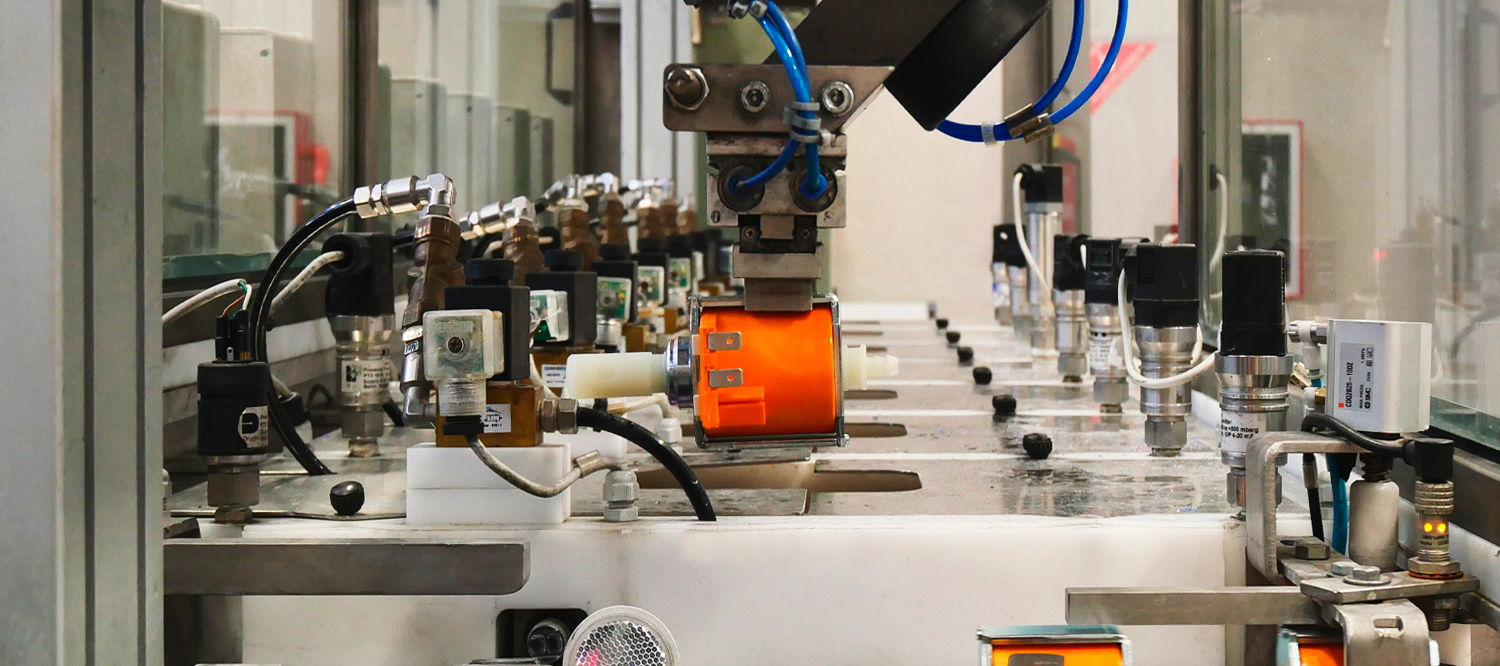
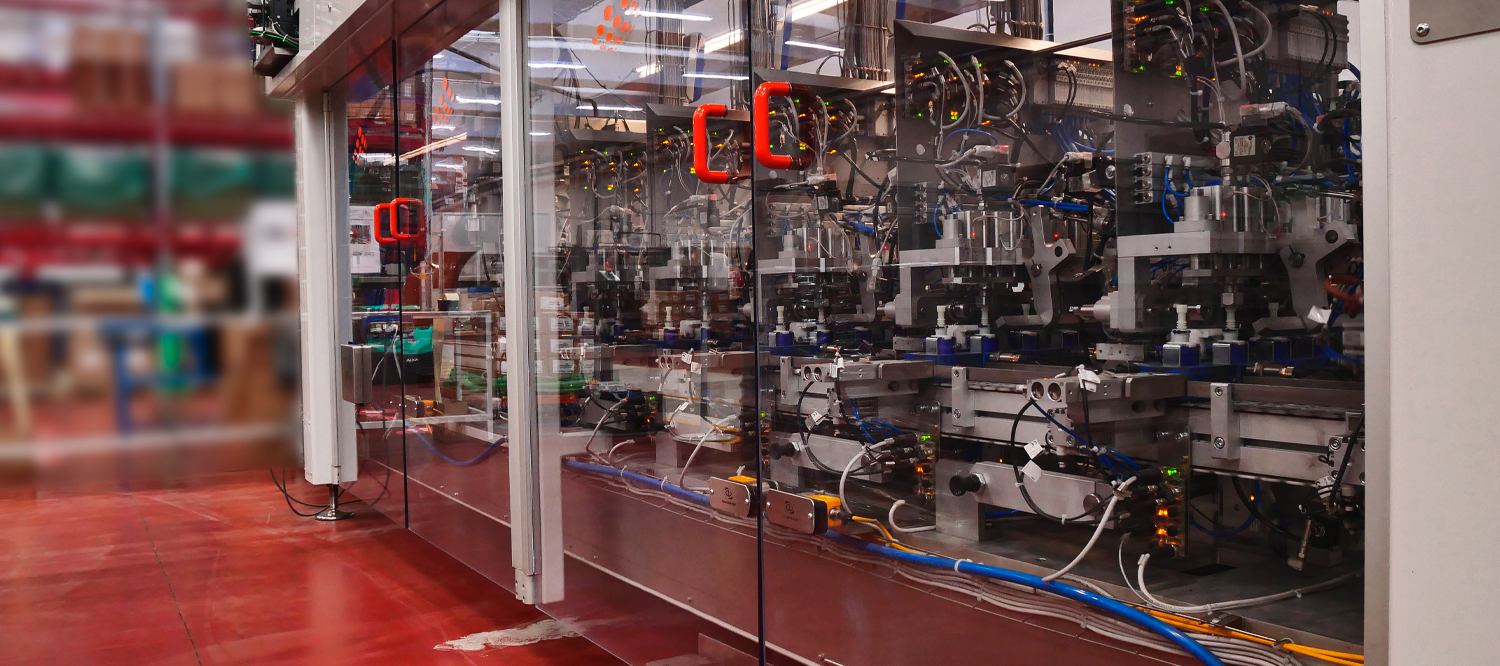
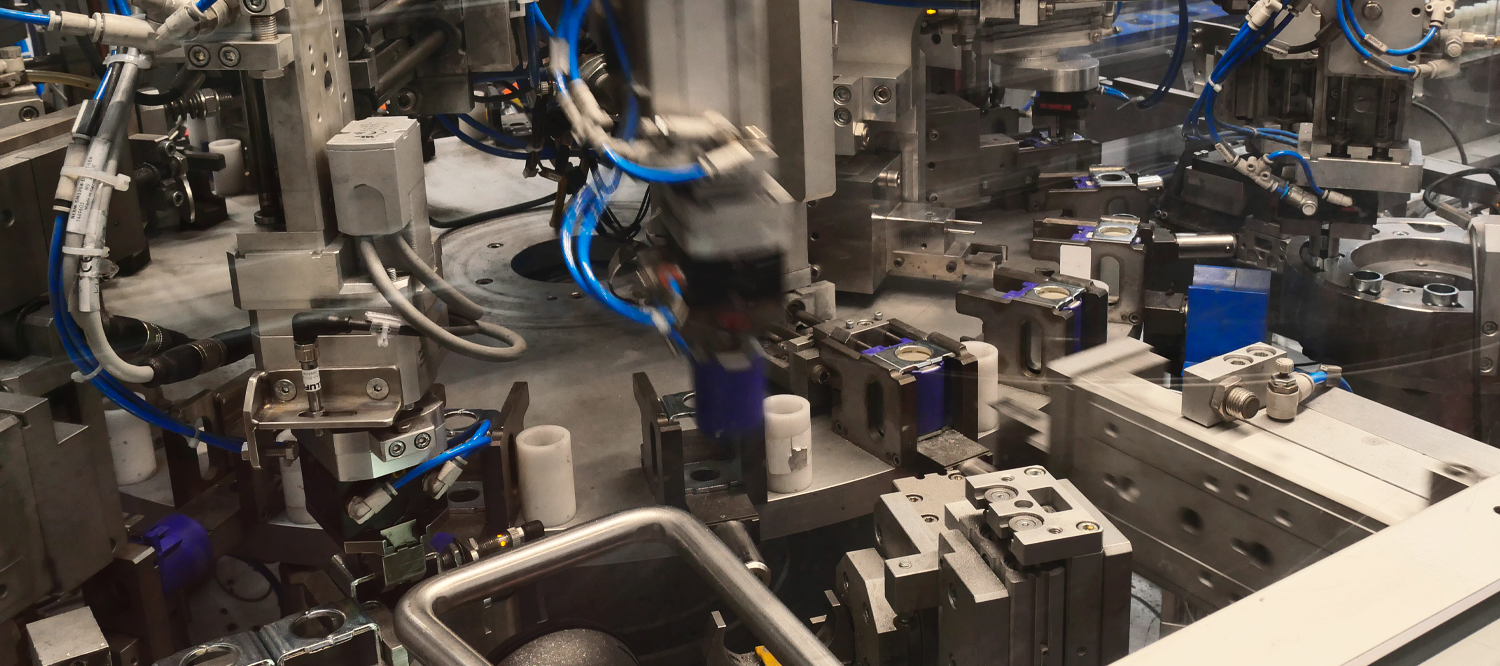
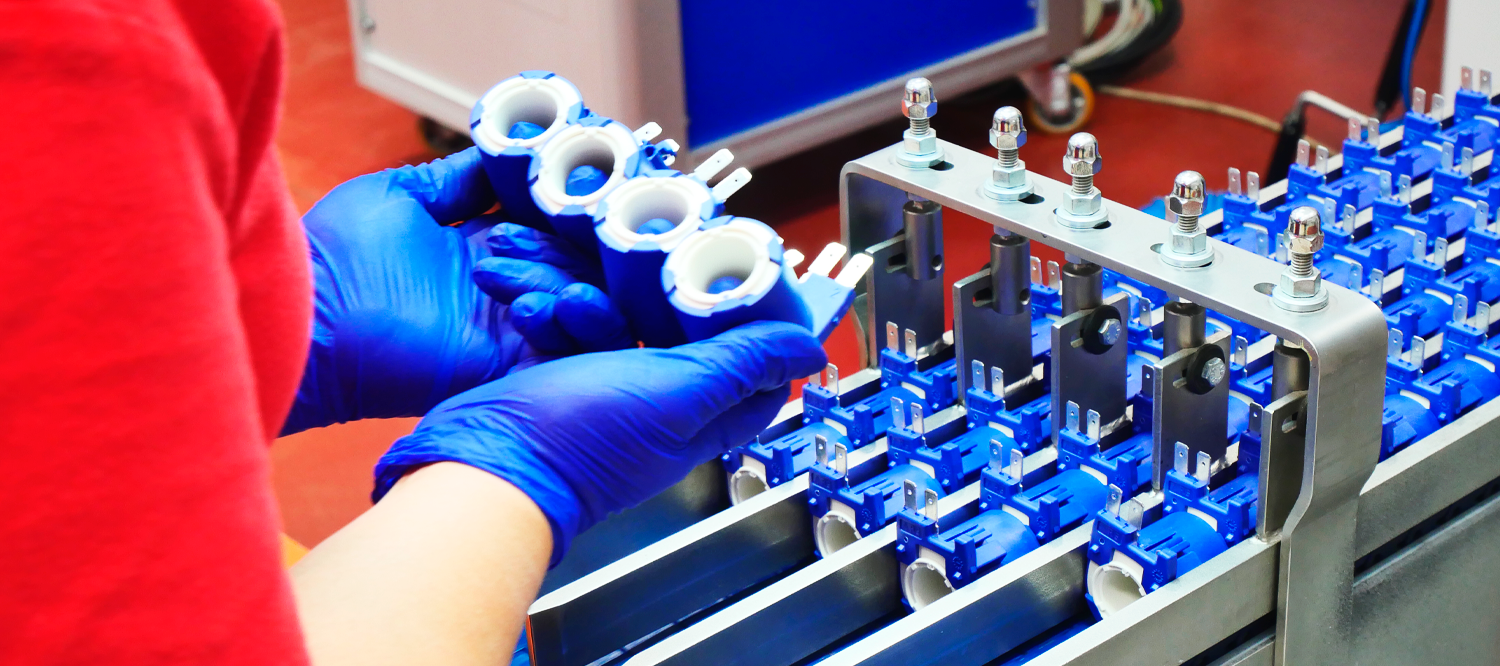
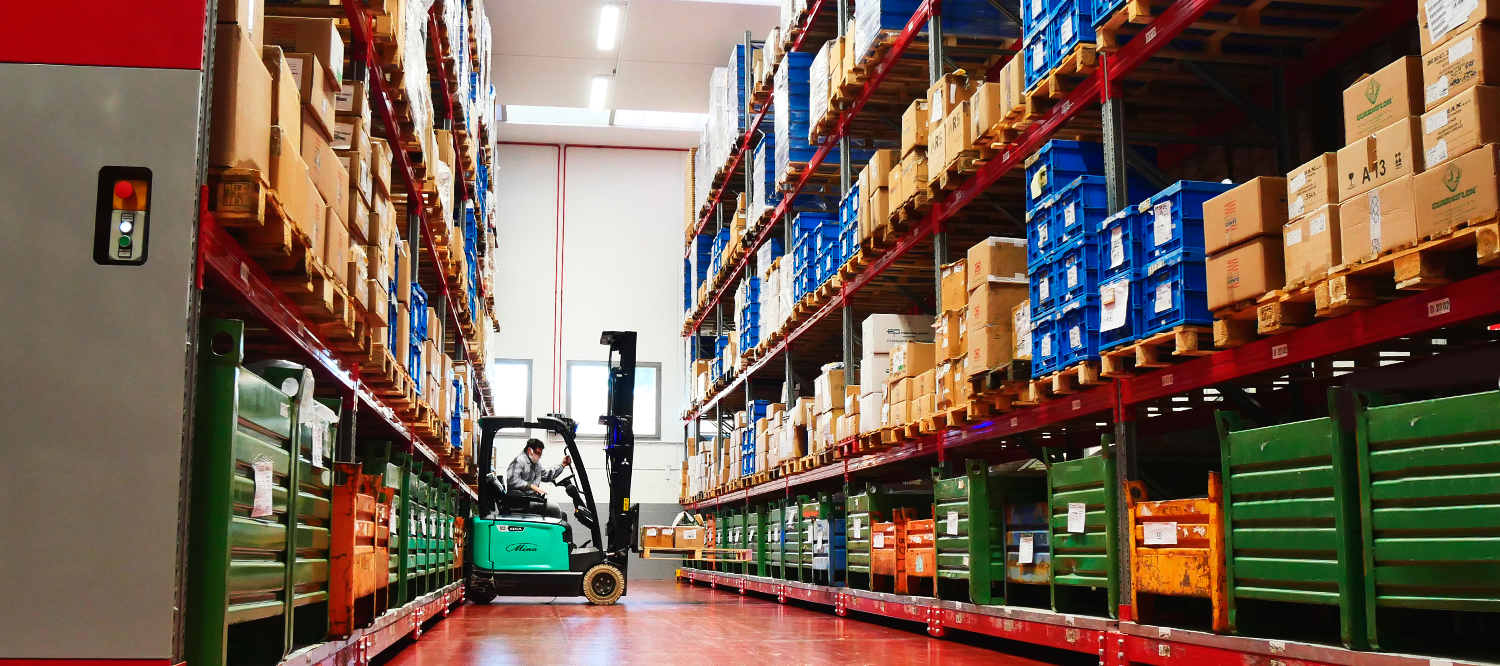
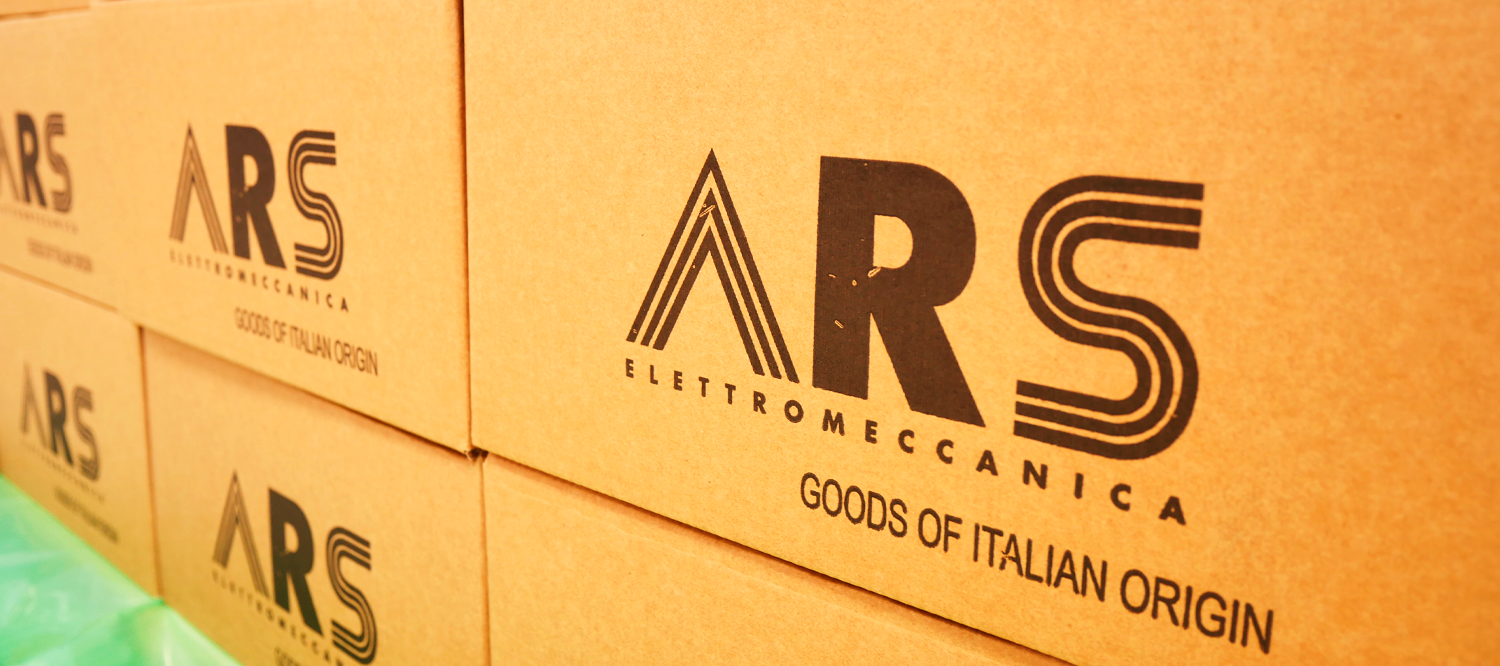
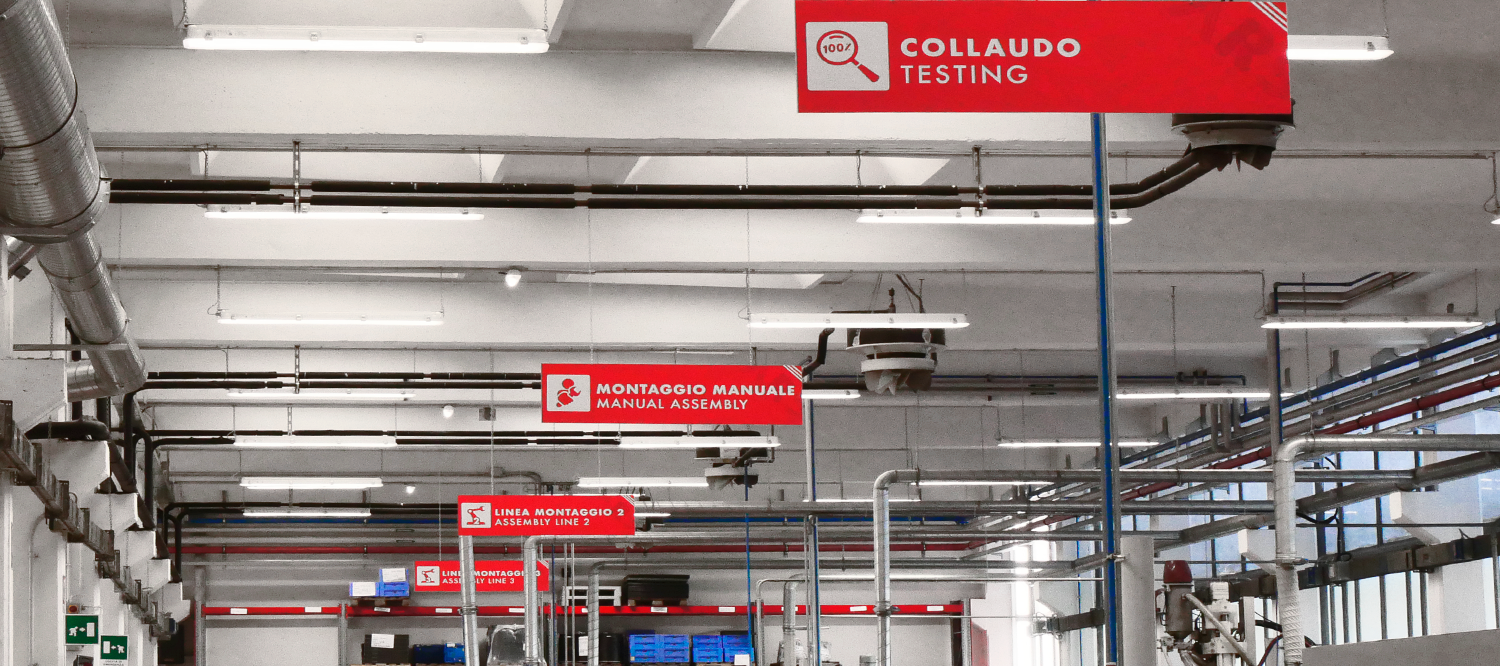
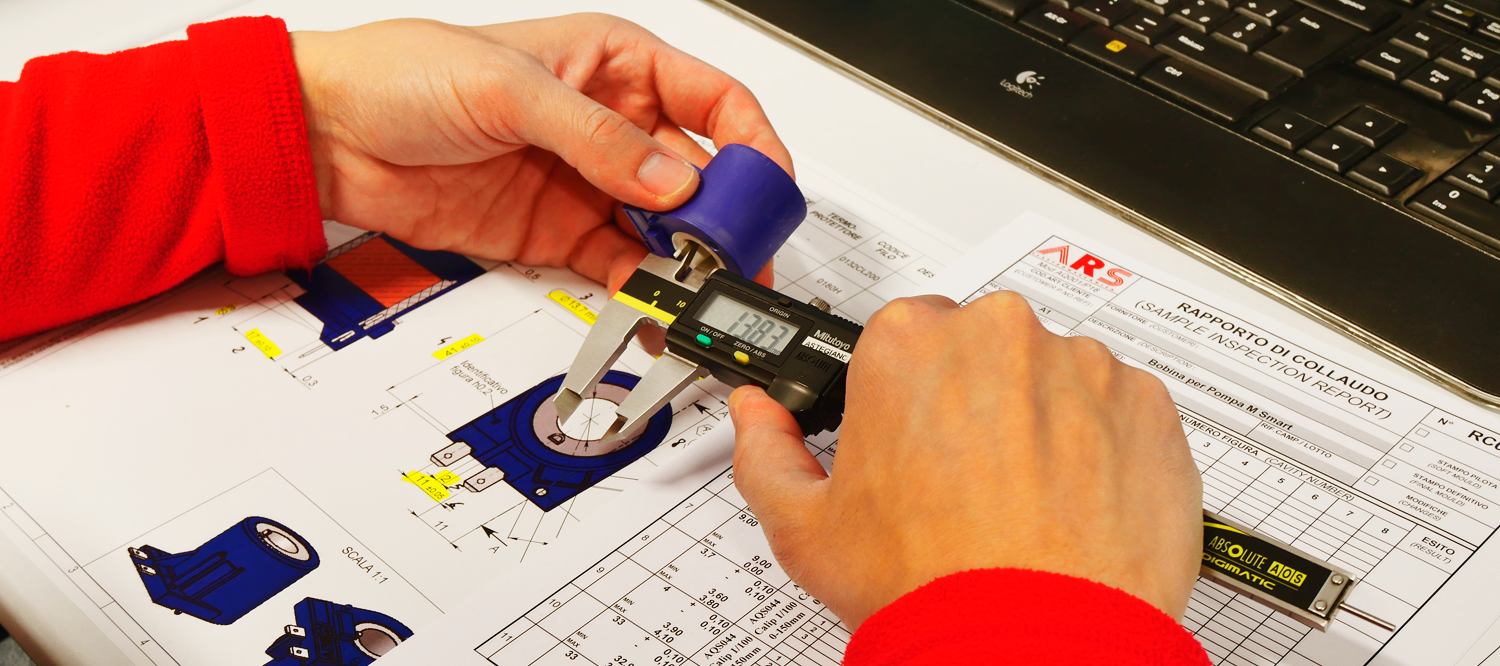
Our production process
Automated machines, automatic assembly lines and a competent and experienced team
Research and development
Our R&D department designs standard and customized products through close collaboration with the customer. All requests from the market are analyzed in order to identify the most suitable solutions in terms of efficiency, quality and reliability. A.R.S. relies on cutting-edge design technology, thanks to the use of CAD-CAM systems and rapid prototyping tools that allow to promptly verify the compliance of products with specifications
Test laboratory
We have a modern laboratory able to perform all the rigorous necessary tests, among which are comprised the ones that simulate the use of products and components under particular stress conditions. The laboratory is equipped with the most innovative cutting-edge tools: profile enlarger, spring dynamometer, test bench for functional and pre-approval tests, soundproofed chamber, climatic chamber and salt fog chamber, pump life test benches, test instrument high voltage (dielectric strength) and 3D printer
Winding and Welding
For the winding and welding of low, medium or high voltage coils, we use machines with a high degree of automation, while for the assembly of the magnetic structure and additional components we prefer manual work. This allows us to have the utmost attention to compliance with all compliance parameters during the assembly phases and to guarantee maximum quality of the materials used in the production phase.
Overmoulding
The plastic injection molding process of our coils takes place on vertical injection moulding machines which, depending on the cases and production volumes, can be equipped with rotary tables with two or more stations and equipped with automatic loading/unloading systems, cameras and monitors for 100% visual control of every part.
Assembly
The operations necessary to put together the various pre-built parts of our products and components are carried out with automated machines and automatic assembly lines managed by expert and qualified technical personnel, to guarantee an excellent and functional final result from every point of view.
Final Inspection test
All components produced by A.R.S. are individually tested with computerized systems that automatically identify the rejects. Surge, dielectric strength and resistance tests are performed on the coils. The pumps, on the other hand, are tested in terms of suction, current absorption, flow rate at specific back pressure, maximum pressure.
Warehouse
A.R.S. has a large and modern warehouse for the storage of raw materials, semi-finished and finished products. An automatic system is installed inside the warehouse to insure intensive space allocation and rational storage of goods. The management control system provides for the easy identification and traceability of all codes and their handling on the basis of FIFO criteria.
Tooling
We have a modern tooling department, equipped with all spare parts and automatic machines for the production of metal parts necessary for prototyping and for the start-up of new products or for updating existing products. The specialists of this department, who carry out technological assignments for the start-up of production batches and maintenance technicians for the necessary interventions on the systems, guarantee the Company maximum self-sufficiency and the reduction of the risks of production stops.
Mold warehouse
All the company's molds (over 300) are stored in a dedicated vertical warehouse where in real time the operators can find information on the location and availability of the molds, in perfect traceability logic, to schedule and verify maintenance to guarantee its constant efficiency of the same as well as to always ensure an excellent state of conservation